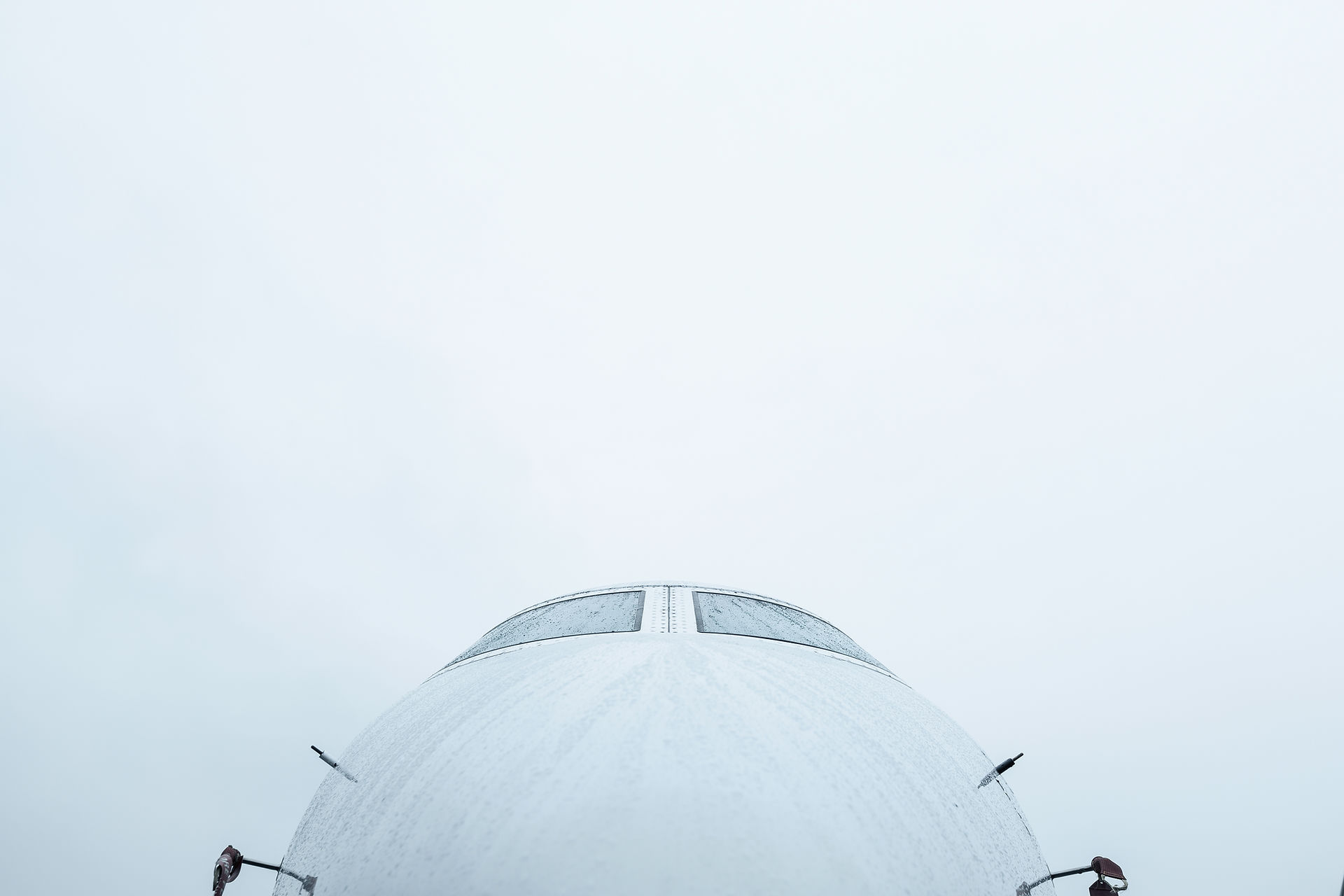
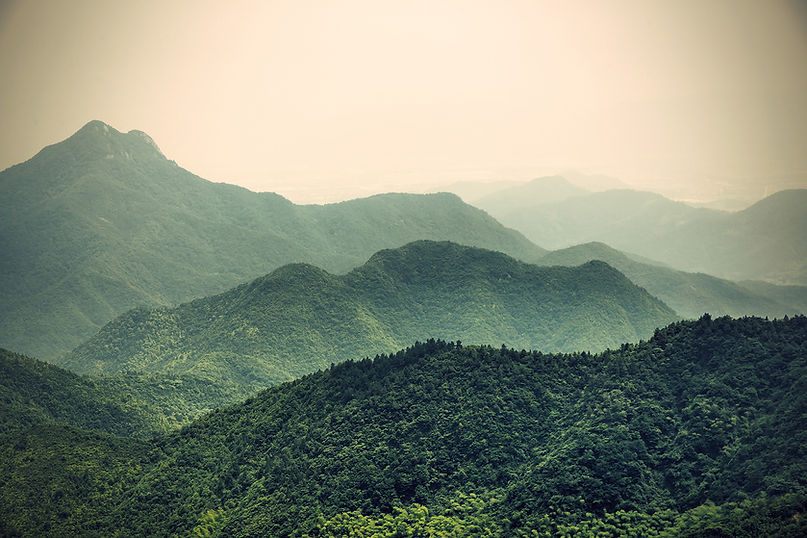
Proceedings in the Life and Work of an
Elk Mountain Home School Student
By Abram Leyzorek,
Twelfth Grade
Abram Leyzorek
November 17, 2018
The Chemical History of Aluminum
Aluminum is an essential component in a myriad of modern conveniences from airplanes to pop cans, prized for its high strength to weight ratio and resistance to atmospheric corrosion. This silvery-white metal was even more highly valued in the time of Napoleon III, more even than gold. However, this was merely for its extreme rarity rather than for its applications in manufacturing. This only changed when two young chemists, American Charles Martin Hall and Frenchman Paul Héroult, standing on the shoulders of other notable scientists before them, discovered a chemical method to economically extract pure aluminum from its ores. Their method was by no means the first to do this, but it was the first to be commercially utilized on a large scale and is still in use today. (“Commercialization of Aluminum”).
However, for thousands of years aluminum was not even known to exist, despite its use in compounds predating 5000 BC. Ancient Mesopotamians used aluminum-rich clays to craft fine pottery. In addition, aluminum compounds were utilized by Ancient Egyptians and Babylonians as medicines almost 4,000 years ago. And from the ancient world to the medieval period, an aluminum compound, known as alum today, was used to bind dyes to textiles. However, it was not until the eighteenth century that anyone suspected that a metal could be found in these useful compounds. (“Hall-Heroult”).
Humphry Davy, an English chemist, made the first attempt to extract this metal in 1807. It was made after a long string of successes in isolating pure metals from compounds, such as potassium from potash and sodium from salt, using a method called electrolysis. (Pizzi). Electrolysis is the process of running a direct electrical current from a battery or other source through an ionic solution called an electrolyte using two metal bars as electrodes. The electrons flow from one electrode to the other making one, the cathode, negative and the other, the anode, positive. Positive ions, cations, in the solution are attracted to the cathode and negative ions, anions, are attracted to the anode. When the ions reach their respective electrodes, electron exchange occurs causing a chemical reaction. In this way pure elements can be separated from compounds. For example, if two copper electrodes connected to a power source were inserted into a solution of molten salt, sodium chloride, the negative chloride ions would be attracted to the anode and the positive sodium ions would be attracted to the cathode. At the cathode, the sodium ions would transfer their excess electrons to the cathode and would become neutral. And the same thing would happen to the chlorine ions at the anode, except here there would be a gain of electrons for the chloride ions. The reactions would look like this: (“Electrolysis”).
At the cathode: Na++ e- → Na
At the Anode: 2Cl- → Cl2 + 2 e-
Although Davy failed to extract aluminum from alum in this way, he satisfied himself that the metal existed and named it alumium, afterwards rechristening it as aluminum. (Pizzi).
The first sample of aluminum was obtained in 1825 by Danish scientist Hans Christian Oersted who heated a mixture of aluminum chloride and potassium-mercury amalgam under reduced pressure. This caused the mercury to boil away leaving an impure sample of aluminum. (Ashby). This chemical reaction was as follows (Caroll, 5):
AlCl3+3k→Al+3KCl
Using a similar process but with metallic potassium instead of potassium-mercury amalgam, German chemist Friederich Wohler distilled aluminum pieces up to the size of pinheads by 1840. From these samples, he determined the properties of aluminum such as ductility, color, and specific gravity. This made aluminum available, but only at the hefty premium of approximately 545 dollars per pound (1852 dollars). (“The Element Aluminum”).
Thus, aluminum remained a mere curiosity until 1854, by which French chemist Henri Saint-Claire Deville had successfully implemented his improvements on the methods of Wohler, namely the substitution of sodium for the more expensive potassium, to produce globules of aluminum the size of marbles using the following method: (“Deville-Castner Process”).
Deville’s goal in aluminum manufacture was to reduce sodium and aluminum’s double chloride, 2NaClAl2Cl, using heated metallic sodium. The natural first step, then, was to manufacture the double chloride. This process was begun by taking powdered aluminum oxide, or hydrate of alumina (Al2O3+water), and combining it with lamp-black, salt, and charcoal. The resulting mixture was then moistened and processed in a pug mill before being extruded through dies, cut into three-inch cylinders, and dried. These cylinders were then precisely heated in an atmosphere of chlorine gas which causes the desired double chloride to evaporate from which gaseous form it was condensed into a pale-yellow, deliquescent material pungent in odor. The reaction that produced this most important ingredient was as follows: (“Deville-Castner Process”).
2Al2O3+3C2+4NaCl+6Cl2→2(Al2Cl62NaCl)+6CO
Translated into English, the reaction is alumina plus carbon plus salt plus chlorine gas equals double chloride plus carbon dioxide.
Now all that had to be done was the reduction of the double chloride using sodium. To this end, the double chloride was pulverized and mixed with slices of metallic sodium before being heated in a furnace along with cryolite, Na3AlF6, as flux. This resulted in the following reaction: (“Deville-Castner Process”).
2 (Na Cl) Al2Cl6 + 3 Na2 = 8 Na Cl + Al2.
This simply means that the double chloride chemically reacted with the sodium to produce the desired aluminum and a byproduct of salt. This alone reduced the price to 115 dollars per pound, but the price did not solely depend on the quantities of aluminum that could be obtained.
The cost of the materials used in aluminum manufacture, a very important one of which was sodium, was a very important factor influencing the price of aluminum. Until 1886 when a man named Hamilton Y. Castner began developing a safe, inexpensive method, sodium production had been very arduous and perilous. Involving electrolysis, the Castner process (completed in 1888) reduced the price of sodium five-fold. Although this development made aluminum more affordable, it was still prohibitive enough to keep aluminum from widespread use. (“Deville-Castner Process”).
These achievements represented giant leaps forward in aluminum production, but the greatest and yet unsurpassed method was still to come. This discovery was twice made independently by two twenty-two-year-old chemists during the same year that Hamilton Y. Castner developed his sodium production process, 1886. Charles Martin Hall, an American graduate of Oberlin College in Oberlin, Ohio,, worked with Oberlin College professor Frank Fanning Jewett to develop the following process: (“Hall-Heroult”).
First, alumina is dissolved in a vat of molten cryolite at a temperature of 982 degrees Celsius (Ashby), acting as a flux as in the Deville process. Then, it, the electrolyte, is channeled into a cell with a carbon-lined cast-iron shell. Carbon anodes are suspended in the electrolyte and the carbon lining acts as a cathode. An electric current is passed through the cell and the dissolved alumina separates into its constituents, oxygen and aluminum. The molten aluminum sinks to the bottom of the cell and the oxygen remains around the anodes. This involves two half-reactions, reduction of the aluminum at the cathode and oxidation of the oxygen at the anode: (“Extraction of Aluminum”).
Reduction: Al3+ + 3e- Al
Oxidation: 2O2- - 4e- O2
These two half reactions can be combined into one whole reaction which is as follows (“Extraction of Aluminum”):
2Al23+O32-(l) 4Al(l) + 3O2(g)
Paul Louise Toussaint Heroult independently discovered this same process just two months after Charles Martin Hall. He applied for and received a patent for it in France and applied for one in the United States in May of 1886. Although this was before Hall applied for his patent in July, Hall was able to prove that he discovered the method before Heroult made his patent application. Two years later, Hall founded the Pittsburg Reduction Company with financial assistance from six industrialists involved in Pittsburgh’s metallurgical market, including MIT graduate Alfred Hunt. That same year, the price of aluminum plummeted to $4.86. By 1993, the price had dropped to seventy-eight cents per pound. And by the 1930s, it aluminum was valued at just over twenty cents per pound. (“Hall-Heroult”). This remarkable figure was not, however, achieved by Hall and Heroult alone.
Two other notable developments aided in the commercialization of aluminum, namely the dynamo and the Bayer Process. Without the former, none of what Hall and Heroult achieved would have been possible. Invented by Siemens, Hopkinson, and Edison in 1881, it provided the power source necessary for electrolysis. Later, aluminum companies moved to places where abundant hydroelectric power could be found to drive the dynamos. While the dynamo and hydroelectricity made inexpensive electricity abundant, the Bayer process cheapened the raw material for aluminum production, alumina. As the Castner process cheapened sodium, the Bayer process cheapened the production of alumina. (Ashby).
Use of aluminum began several millennia ago in pottery and medicine, but it was not until relatively recently that it was discovered. Over the years, better and better methods were devised for aluminum production and the production of ingredients involved in its production. This continued until the price, once greater than that of gold, was reduced sufficiently so that the full of industrial potential of aluminum could be realized. This was achieved in large part by the work of Charles Martin Hall and Paul Louise Toussaint Heroult in 1886. (“Hall-Heroult”). These young chemists were heirs to the work of several other notable chemists who made important contributions to the field of aluminum including Humphrey Davy, Hans Christian Oersted, Friedrich Wohler, Henri Saint-Claire Deville, Frank Fanning Jewett, Hamilton Y. Castner, and Karl Joseph Bayer. Standing on the shoulders of these intellectual giants and using new technologies of their day, Hall and Heroult were able to make aluminum available for widespread use.
Works Cited
16.7: Electrolysis: Using Electricity to Do Chemistry. (2018, May 4). Retrieved November 11, 2018, from LibreTexts.
Aluminium and Its Manufacture by the Deville-Castner Process. (1889). Science, 260-262.
Ashby, J. (1999). The Aluminium Legacy: the History of the Metal and its Role in Architecture. Construction History, 79-90. Retrieved from https://www-jstor-org.www.libproxy.wvu.edu/stable/pdf/41613796.pdf? refreqid=excelsior%3Af258906f5aaf47b4f874f03071206939
Commercialization of Aluminum. (2001, November 2). Retrieved November 11, 2018, from acs.org: https://www.acs.org/content/dam/acsorg/education/whatischemistry/landmarks/aluminumprocess/commercialization-of- aluminum-commemorative-booklet.pdf
Dr. William F. Caroll, Jr. (2012, April). From Garbage to Stuff: How we Recycle Plastics. The Alembic, 39(3), p. 5. Retrieved from https://www4.uwsp.edu/chemistry/acscws/39%20-%203%20April%202012.pdf
Education, T. J.-O. (n.d.). The Element Aluminum. (G. Steve, Editor) Retrieved from Jefferson Labs: https://education.jlab.org/itselemental/ele013.html
Extraction of Aluminium - Hall (Electrolytic) Cell. (n.d.). Retrieved November 11, 2018, from mypchem.com: http://mypchem.com/myp10/myp10_htm/al_ext.htm
Pizzi, R. A. (2004). Humphry Davy, Self Made Chemist. Chemistry Chronicles, 49-51.
Production of Aluminum: The Hall-Héroult Process. (2018). Retrieved November 11, 2018, from American Chemical Society: https://www.acs.org/content/acs/en/education/whatischemistry/landmarks/aluminumprocess.html